Three weeks ago I fitted the 12 mm ply sides to the hull and then took a week break to drive to Buderim for some minor civil engineering work at or No 3 son’s home. The break was a healthy one with plenty of exercise and fresh air and it was time for a break from sawdust and epoxy. On return to Sydney I was slowed down by a virus which was neither Covid nor Influenza A or B. Despite a negative diagnosis it was not a bug I wished on anyone so I had a quiet week confined to the boat building site.
The first of the jobs tackled was glassing in the chainplate frames with five layers of double bias of which two are over the whole frame. The frames are angled in line with the spreader angle so one side is easy to work on and the acute angle side is a big awkward. While in the epoxy glass mode I completed all the internal glass joins to get the itchy jobs out of the way. As careful as I was I failed in my endeavours to keep my clothing glass free so for comfort sake I put the glassing clothes aside and started afresh with new clothes and a resolution to be even more careful.
So far my care has worked as the glass had been trimmed and sanded successfully.


The next task was to bog in all the shelves on at least one side so that after turning the other side can be completed easily. Once the shelves were horizontal and stable it was time to prime all the bare plywood internals.


Priming the internal plywood had not been on my construction plan but the bout of continual wet weather we had earlier in the year convinced me that the bare plywood had to be primed to protect the timber from the dreaded mould that was growing in every home in NSW. Now the weather had improved greatly but once set out on the journey to prime the timber it was a journey that needed to be completed.
As well as bogging in the shelves all the bulkheads and stringers had to be filleted in with structural epoxy bog before the priming could be started.
Having decided on a fillet size I prepared a test piece to satisfy myself that the structural strength was satisfactory. Being confident I had completed all the filleting before the test piece was cured enough for the test. It passed with the plywood test piece breaking instead of the fillet.
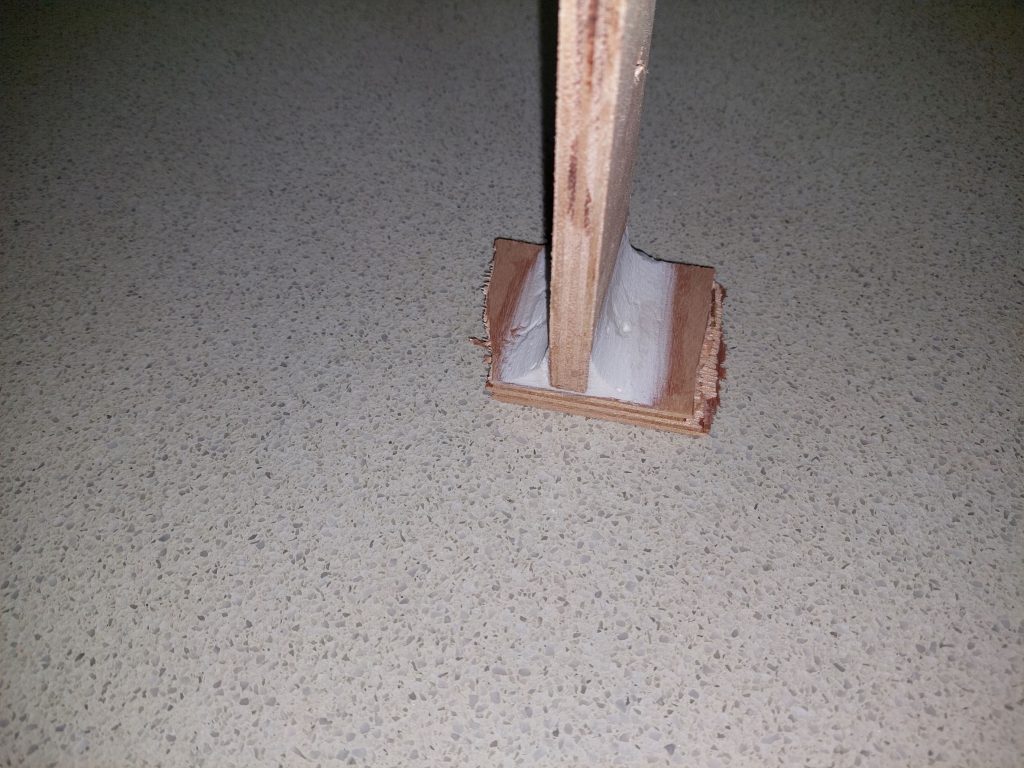
Doing structural fillets is an acquired skill. As simple as it looks it takes time to master the techniques and do the work at an efficient pace so some of my fillets are excellent and some needed a lot of post cure surgery before they were tidy enough for painting. As time progressed my speed and quality improved so that the finished job looks fairly professional.
A lot of the fillets will be hidden inside cupboards but the perfectionist in me refused to do these to any lesser standard than the ones in full display.
It takes a day to sand from the mast step to the transom on one side and then apply one coat of primer so there has been four very big days sanding and painting to get the two coats applied.


After the first coat the sanding back reveals any defects that need more preparation and the first coat brings up the wood fibres which need to be removed before the second coat is applied.
Planning ahead I prepared some of the internal ply that up to this time only a single coat of primer so that any left over primer could be used efficiently on a second coat and that has worked well with nothing wasted.
At the bow I have three bays which have the first coat of primer and are sanded back ready for their second coat. I think that is the next step and that will use up what primer I have.
Next job is to do all the packing pieces between the keel floors and the hull so that when I affix the bottom ply the internal work is complete. To be prudent there is probably two weeks work in that exercise .