Next Passion
At Greenwich Flying Squadron we have enjoyed our share of good fortune out on the race track and currently lead the twilight series in the depleted Black Fleet.
I am hoping that the Beck team will turn up for the series but understand that with a team of MC38s to train against our twilight is more of a social event.
Our results are a combination of starting the series with a good handicap and making appropriate sail selection topped off with a dose of good wind shifts.
Last week we were second to Ausreo on handicap and while we expect Ausreo to go well in 20 knots of breeze not even an optimist would have picked Passion X to lead the fleet around Goat Island and back to Cockatoo. We can credit the last minute genoa change for the No 3 Jib for that. Consequently we were only mildly out of control for the first half of the race. As the breeze abated the regular order was reestablished but we had time up our sleeve except for Ausreo.
So why did we get a second again this week. Well the No 1 heavy that we so hurriedly took down last week was still in the V berth and had to be folded sometime. That was the basis of the selection and to compensate for the flatter genoa we left the backstay very loose for the evening. Admittedly the regular order was established right from the start but we hung on to the rear of the fleet on the beat to Goat and made up a little ground on the run back to Spectacle Island. Along the Hunters Hill shore we were not in phase with the lifts and knocks but then again most of the fleet was suffering the same fate so we lost little time to Agrovation, Meridian and Joli while out in front with a freshly applied antifouling was Utopia followed by the reliable Jackpot.
Humbug is the last throw of the dice and we threw a double six lifting all the way to the finishing line. Having eyes only for the ribbons on the genoa I did not realise that Meridian and Joli were not that far ahead and so as we crossed the line our hopes for another good result were high.
Bonus points was a good photo of Passion X on the GFS facebook page.
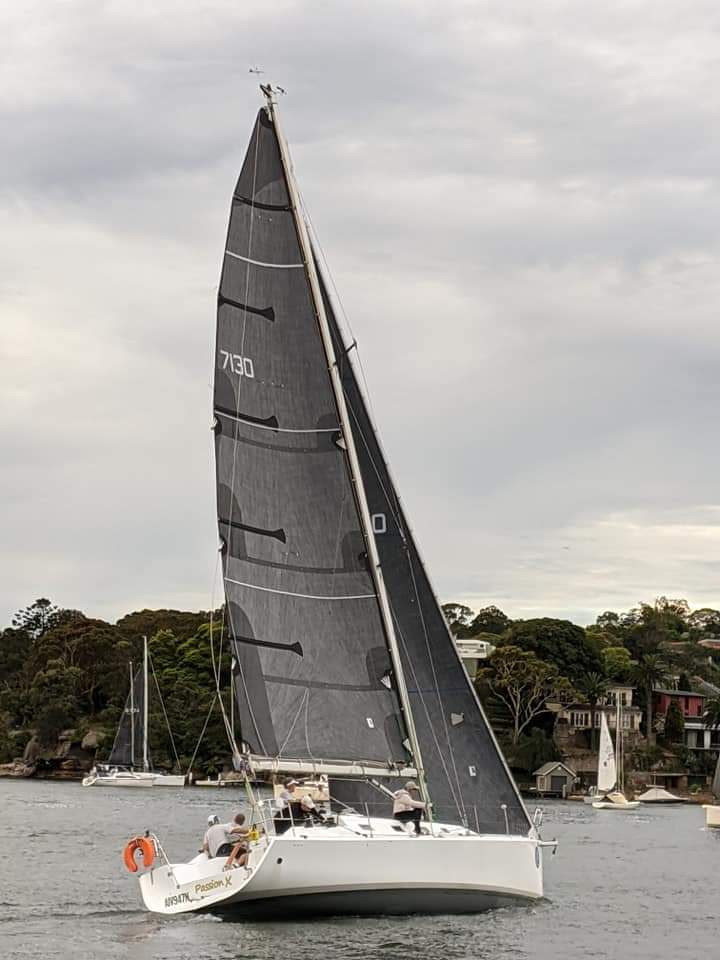
With help from grandson Otis the last of the large heavy bulkheads have been mounted on the building frame. With a mighty effort by Tuesday evening we mounted the six remaining bulkheads to complete the heavy lifting.
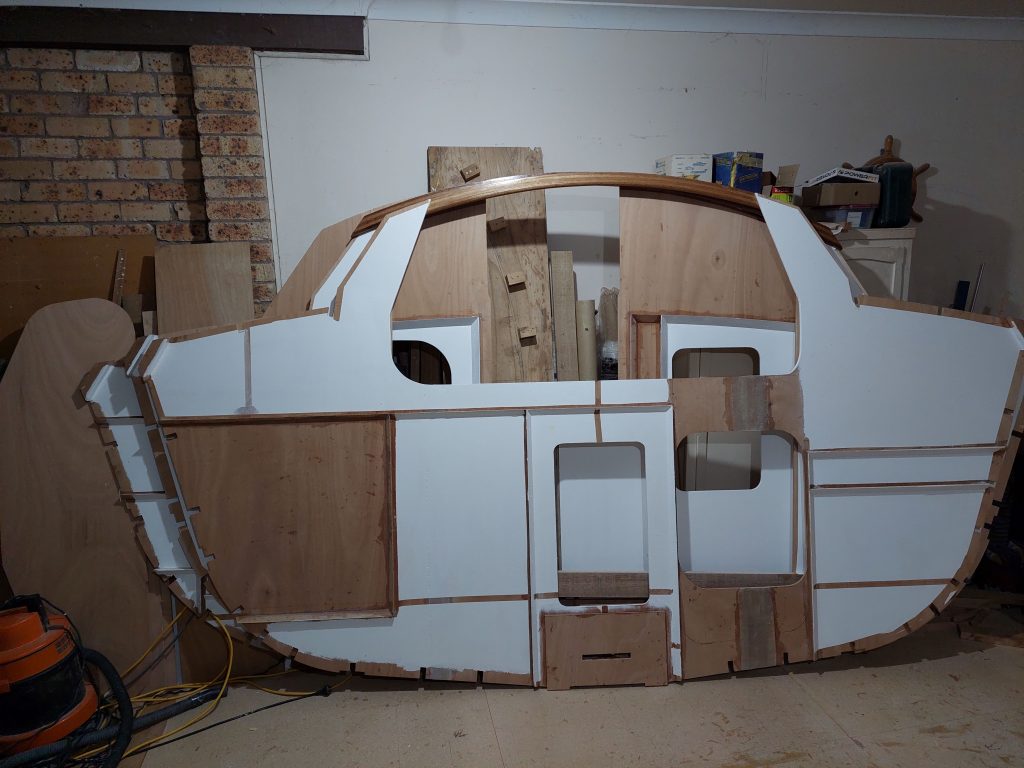
In the gloom of the evening I checked the alignment with the laser level while giving the local mosquitos a good feed.
Wednesday morning I revisited the alignment and noted the keel centre line was not exactly aligned. To help with this final check I used the laser level to true up a plank that could be temporarily laid down the keel centre line and completed the alignment.
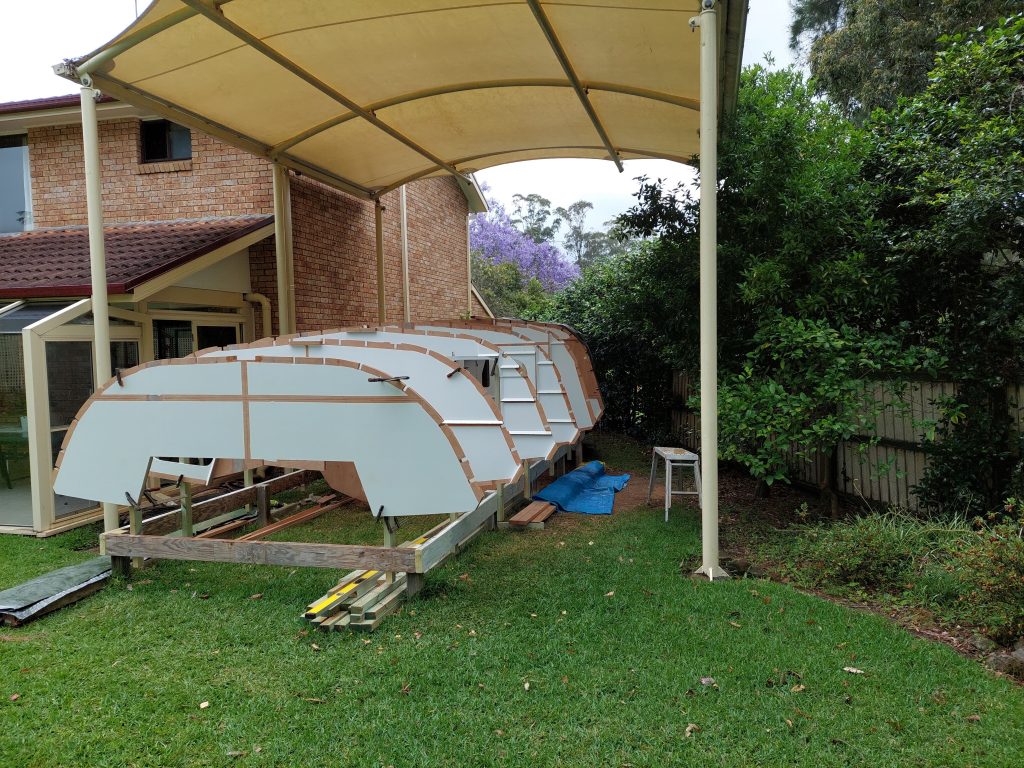
It helps considerably to have fitted all the furniture cleats on the workshop floor as these provide a good reference.
The next stage of the build is fitting the stringers so Thursday was spent cutting large planks down to 32 by 22 mm sections for the tangent stringers and cutting 12 mm plywood into 100 mm wide strips where the flat sheets of plywood will meet the curved moulded plywood chines..
With a good soaking forecast I used the stringers cut temporarily hoping to get a cover over the stern. Alas the rain came too soon and too strong for any meaningful progress.
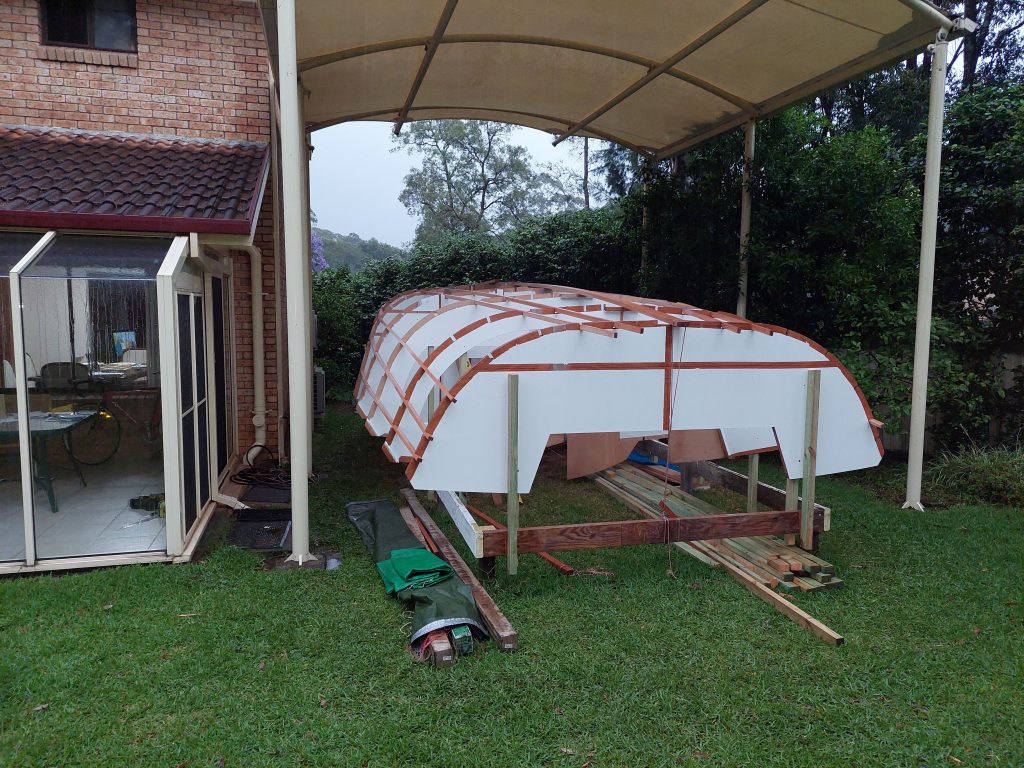
Today despite the frequent showers I cut enough of the main 44 by 22 mm stringers to fill the empty slots in the stern and get a cover over.
So hurried was the process that I did not have time for photos before pulling covers over and retreating from the rain.
Despite the lack of evidence I can report that I am happy with the alignment of all the stringers and she looks very fair and true. On my last build I played with the stringer alignment to get a fair line on them all. This time Dudley had provided much more comprehensive stringer location information so provided the frames are in the right place the stringers will be fair.
Surprisingly we have made reasonable progress on cutting timber. The strongback and gunwales are already cut and the scarf joins prepared. All the tangent stringers are cut and most of the plywood for the tangent stringers. Then about 20% of the main stringers have been cut so there is plenty to do if the rain persists.
My target for this week was to have all the bulkheads mounted and that is done. As for a target for next week that will depend on the weather but I think that I should be able to finish cutting all the stringers.
Since the timber for mounting the bulkheads to the building frame arrived on Tuesday I have mounted on average 1.2 bulkheads a day. Allowing for a day of rest that works out to exactly one bulkhead a day. This might not seem stellar performance but I have also been completing two coats of epoxy primer on each side of the bulkheads prior to mounting. During the week I did a couple of 9 hour days of painting and sanding as well as mounting a bulkhead.
The procedure seems to have settled down to one of mounting a bulkhead with clamps and checking with the laser level before screwing it to the building stock for the duration of the build. Inevitably after the laser level check there is a small adjustment to do the following morning before starting on fitting the next one.
I have fitted all the light bulkheads and from now on it is a two man lift.
Today I would normally go to Gosford to sail the Laser but with a forecast of 5 knots and a very wet Sunday on the way I decided that the priority was to get a tarpaulin over the frames that extend out in front of the awning where I am doing the boatbuilding. That meant finishing the bow instead of installing one of the largest frames. As a bonus I used the front section of the strong back to hold the frames together so that from the bow it is starting to look like a yacht.
Everything has to be done sometime so I like to do tasks when they will add the most value to the progress. Todays tasks included taking the masking tape off the three frames painted last night and shuffling the bulkheads around so that “F” could go on the garage floor for the final reinforcing piece for the engine bed. This is an important frame as it is at the aft end of the keel and takes the grounding loads from the keel. The top of the strongback goes through a 192 mm wide 21 mm deep slot to form a very solid I beam with the 30 mm deep 300 mm wide strongback. When I say it takes the grounding loads I should explain that the I beam ties together the rear three keel floors and the combined three floors take the grounding loads but the keel floor attached to bulkhead F is in the middle.
The next task was to prepare the forward part of the strongback where it bends sharply down to the stem. On the previous yacht I cut half of the keel off and scarfed in a replacement piece as it is easier to bend two 15 mm thick planks than one 30 mm plank. This time because the strongback is narrower at the bow I used the bench saw to cut halfway through the plank sideways and then turn it over and cut the other half. As the plank became wider I did each side in two passes so as not to overload the motor. Once cut from station Zero all the way back to bulkhead A I cleaned up the cut with the hand saw. The whole process was remarkably quick and the slot is clean and ready for gluing back together once bent into the final shape.

Somewhere in this exercise I used the laser level to do a final check in bulkhead E and moved it 2 mm sideways and 2 mm down to its final building position.
With all the preparation out of the way I became a carpenter for the afternoon making up a temporary frame off the front of the building frame to hold the bow. At the same time I could chat to the neighbour who was watering his garden despite the forecast of a downpour tomorrow.

There is a deal of satisfaction when all the elements line up as they should and by 6 pm Elaine was giving me a hand to pull a tarpaulin over the front frames in time for tomorrow’s rain.
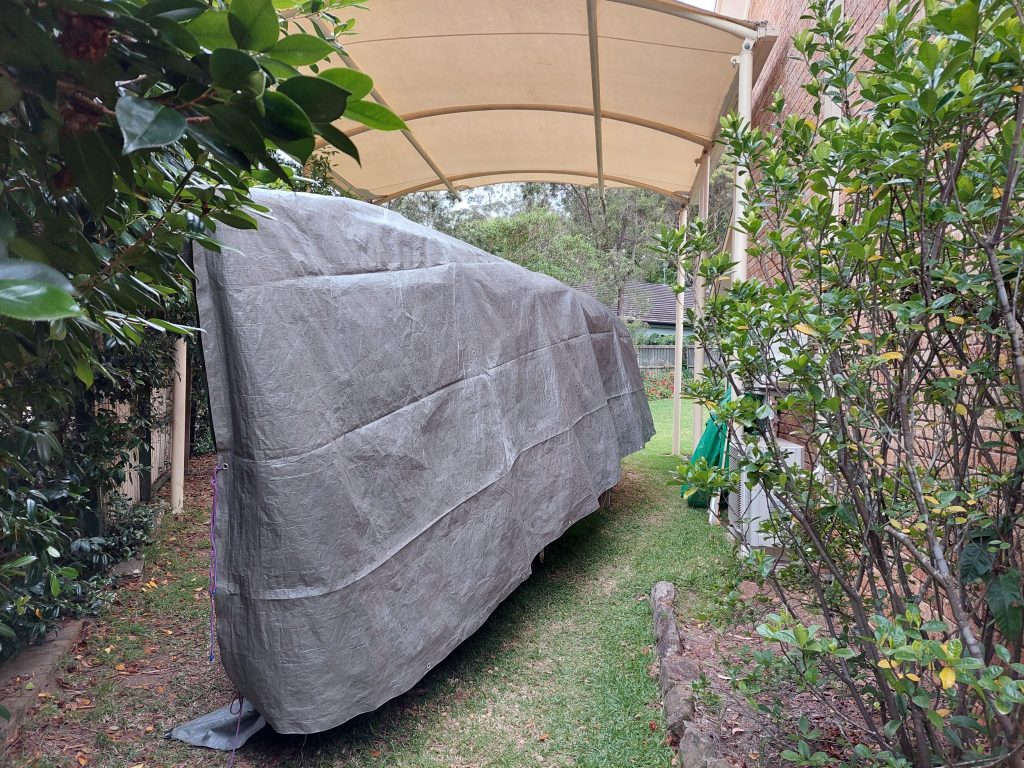
Despite the wet weather forecast it is a Club Championship at Middle Harbour Amateur’s tomorrow so it will be a day of boat building.
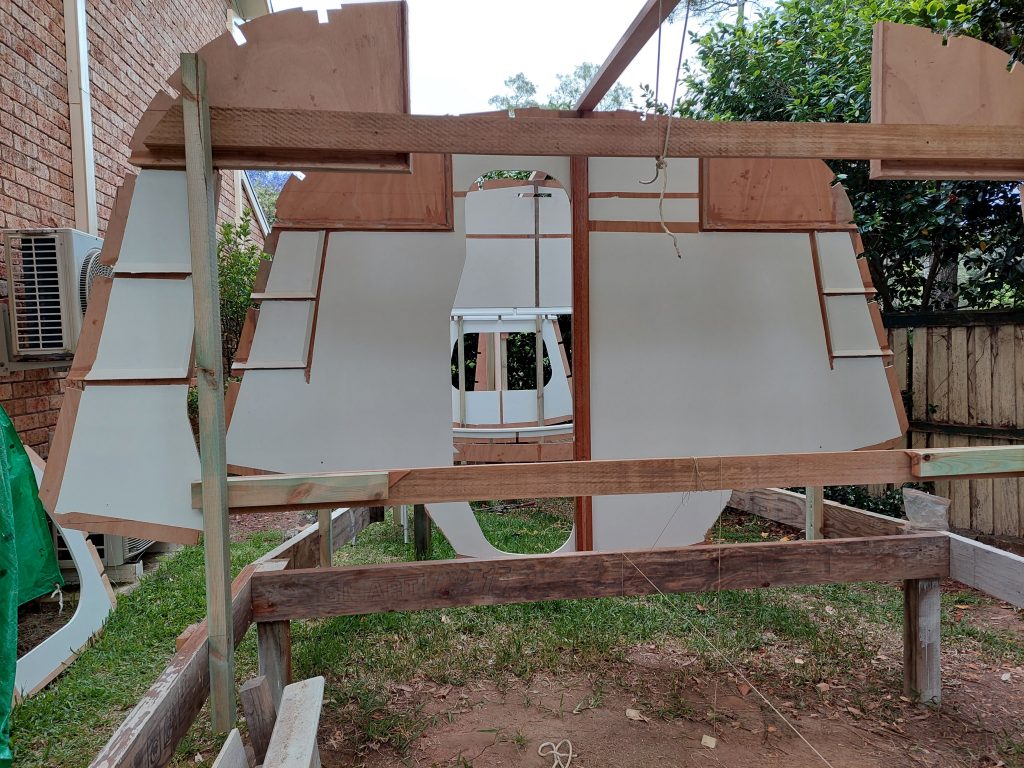
Saturday is normally a sailing day when I hitch up the Laser and head to Gosford but I have had a bit of a frustrating week with my mega project so that took a higher priority. The tasks for the day were not overtaxing but fate had other plans.
Before I could prime my transom to protect the timber from the weather I had to router a 48 mm wide 12 mm deep slot for the knee. Just a few minutes into this task and the faithful old Ryobi router died. It had a good life building a lot of yachts and I possibly pushed it a bit too hard but these are handyman tools, not life long assets.
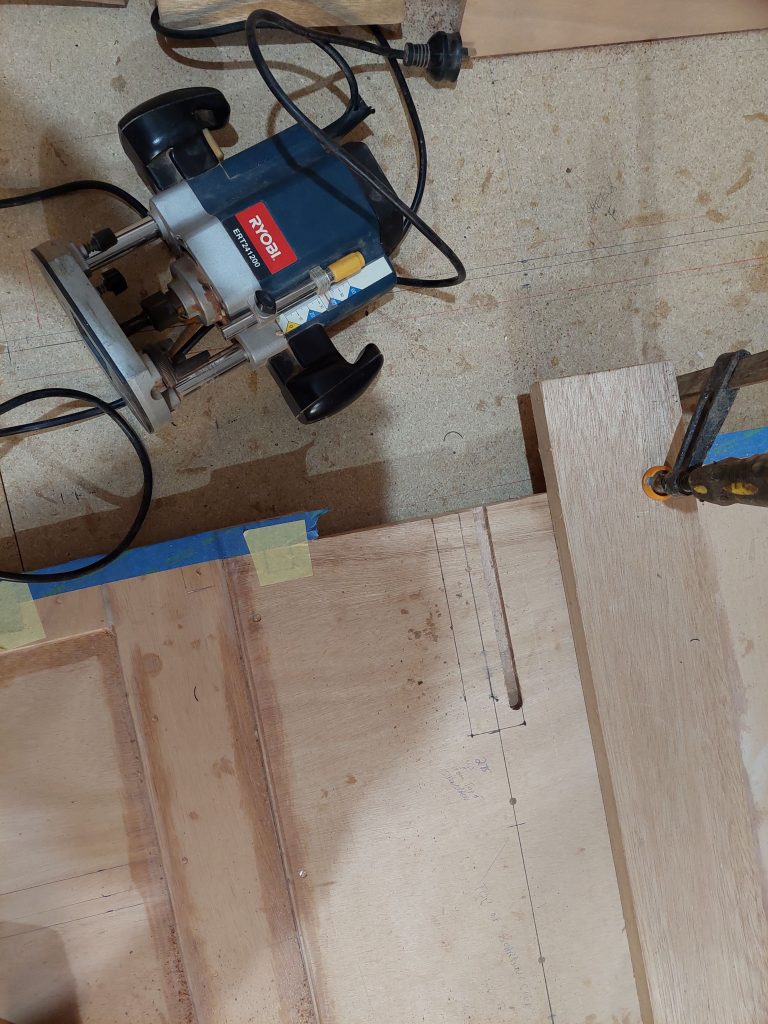
A quick trip to Bunnings secured a new, more powerful one but one that fitted my router table well.
Armed with new router and a new found respect for looking after it I soon finished the three tasks, the transom, the mast post and the stem bulkhead.
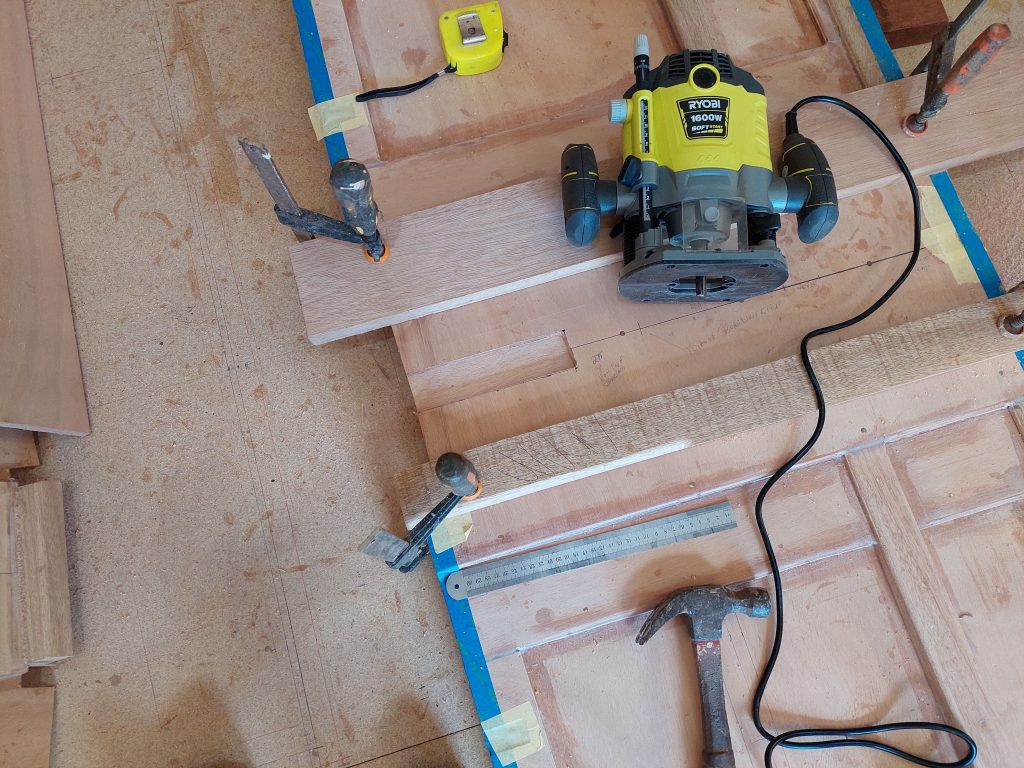
The stem bulkhead needed further attention as I had to move the station position 12 mm from where I had planned to mount it and that meant a 4 mm trim to the shape. In the calm of Friday evening post the Balmain afternoon pursuit race I set up the stem bulkhead on the kitchen bench and carefully remarked all the positions for the new trim line. That done the execution on Saturday was a mundane if careful task.
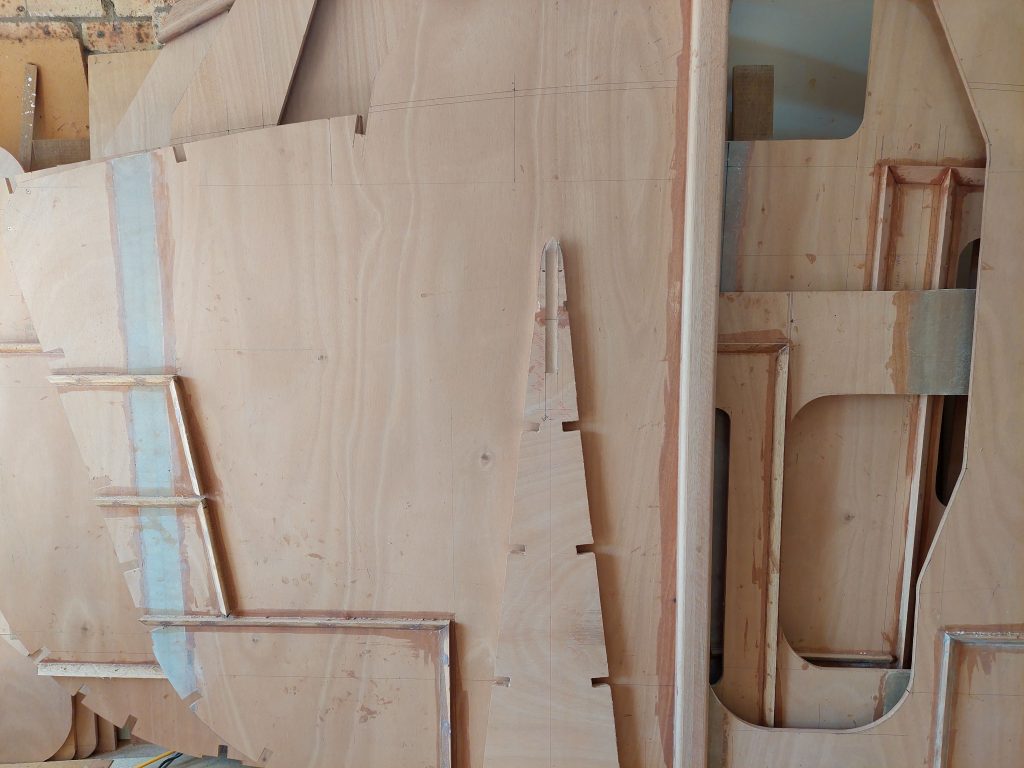
The dilemma before me was whether to epoxy saturate the laminate cabin beams to protect them during the construction of whether to start the epoxy primer surfacer on the plywood bulkheads.
As it was a warm day and good for epoxy work I opted for the epoxy saturation first as I could stack the frames and do multiple laminated beams where the white epoxy primer would need shuffling around on the front lawn.
With three bulkheads stacked on the garage floor I was able to get the rest away for the weekend and will leave the white epoxy for another day.
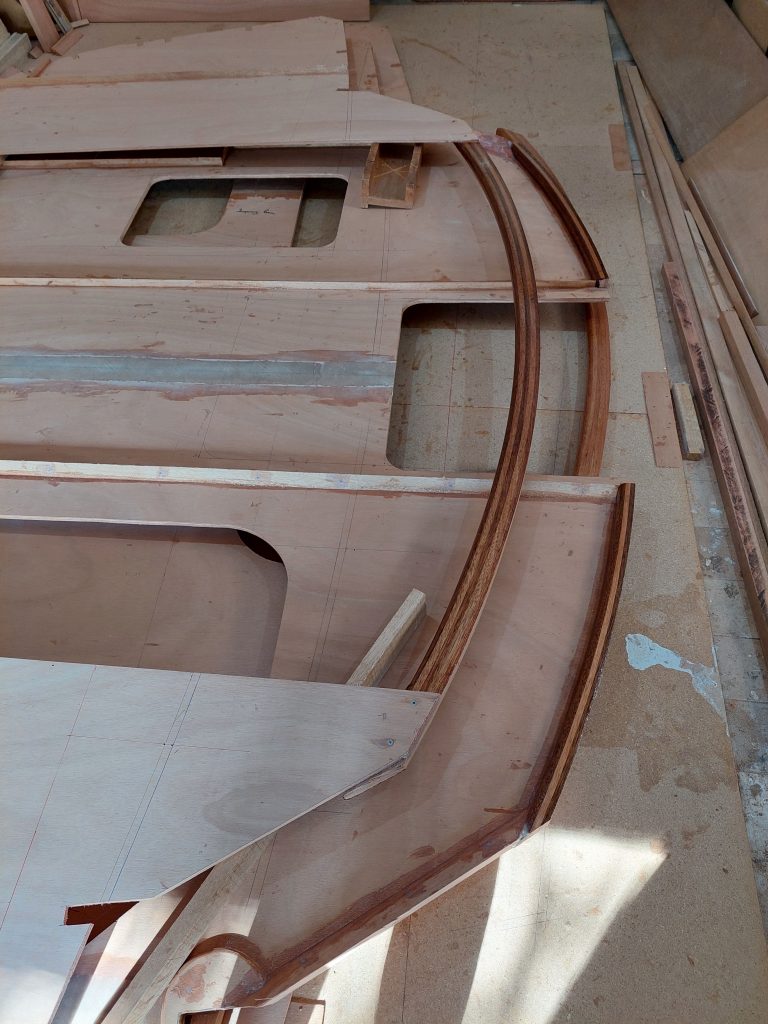
Meanwhile out on the lawn and out of the garage to give me some working room were bulkheads waiting for white primer which never came today. Perhaps Monday will be kinder to these bulkheads
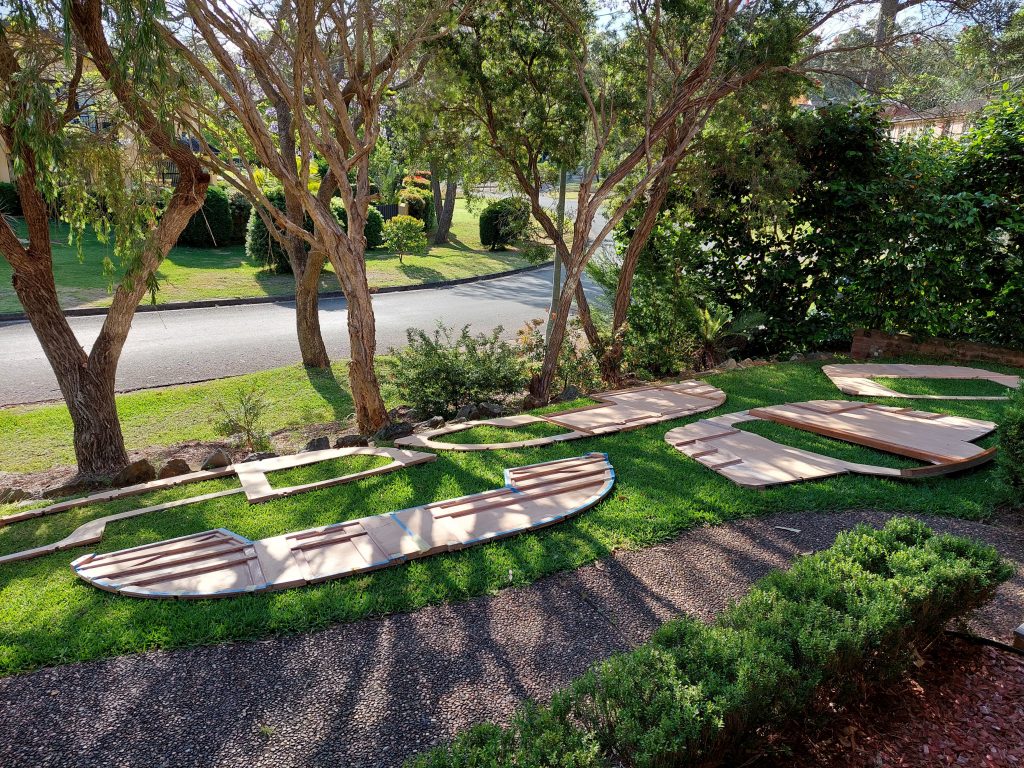
Another Friday afternoon at Balmain and another windy day. It seems that the No 3 jib has been the only headsail to see the light of day. That is not exactly right as we had the No 1 light up for one twilight race but apart from that the Carbon Sports No 3 has been the only headsail used.
With the appropriate level of caution we left the reef in the main from last Wednesday night and made good progress in our pursuit of Irukandji and Odyssey.
Irukandji with a full main started to pull away on the run back from Goat Island so we took out the reef to try to keep up. That worked for the downwind portion of the race but once back on the wind the breeze increased so we struggled with the extra sail area.
Avalon did catch and pass us and we never caught Irukandji so it was a fourth place out of a diminished fleet of six yachts.
I don’t mind sailing with the No 3 jib. It has a very nice shape and covers a reasonable wind range. Also it is good practice for the new Passion that is under construction as she will have non overlapping jibs although about 30% bigger than Passion X
The second night of our twilight series was a windy one with plenty of action so it is not surprising that there are no photos on the Greenwich Flying Squadron facebook page. Sweet Chariot and Passion X opted for a cautious rig with small jibs and a reef in the mainsail and were rewarded with second and third place on handicap. The permanently reefed Ausreo with a lot more weight and waterline took the handicap prize which in the conditions was to be expected.
Third place was what we expected given that we were close to the front of the feet and at the half way mark were mid fleet on fastest times.
Our small crew did well under the circumstances and we did have a little luck with the phasing of the shifts around the healands.
Back at the garage most of the bulkheads have been finished and the final touches may happen tomorrow.
Planks of Meranti have been selected for the backbone and all the timber for the gunwales has been cut. I did make up a giant mitre box for cutting the splice angles on the 32 by 100 mm timber but I will need a much longer saw to be able to use it. On Passion X the Makita power planer was used to cut all the splice join angles and I am still experimenting with this one.
When the weather is right I have a stock of timber to cut into 22 by 44 mm stringers so there is plenty to do.
I have been getting a bit ahead of Dudley Dix who is designing my new dream racer cruiser to the ISO standards. Dudley has other clients to serve and believe it or not he has another life with his yellow Lotus Europa and his surfing passion. That said he has been very responsive and making good progress.
While waiting for confirmation on some of the vital statistics I have spent time installing as many structural cleats and furniture cleats as seems practical. That includes optional cleat for removable floors in some cupboards where I will be routing the services This is not needed for functionality but for appearance, not that anyone but me will look into the bottom of a locker looking for a tiny removable floor. However with time to spare I have been adding little finishing touches.
When it comes to finishing the random orbital sanders that I discovered during the Passion X project have been put to good use finishing the sawn surfaces of the triangle cleats so that there will be much less filling and sanding at the end of the project.
One of the benefits of building a second time is to know what surfaces need some minor details differences whether for comfort, durability or just plain old appearances. I have to confess the latter one does exercise my mind a lot as I like the aesthetics of cleats finishing at some visual logical end point rather than just the functional one.
Today my only task has been to fit the 32 by 32 mm triangle cleat that joins the deck and the bulkhead. It is fine Meranti and quite stiff so I have left the cleat as one long length for ease of bending and after the thickened epoxy has cured I will cut out the center section where the deeper cabin hatch goes down to the cockpit floor level. The clamping arrangement for a triangle cleat is a bit agricultural so I will leave it to cure overnight and go sailing this afternoon. That will leave me just a few 20 by 20 furniture cleats to finish this last bulkhead before shuffling the deck again for a final check.
Not too shabby considering the plywood arrived 4th September and we did not have plans at that stage. Did I hear you say “Well done David and Dudley”
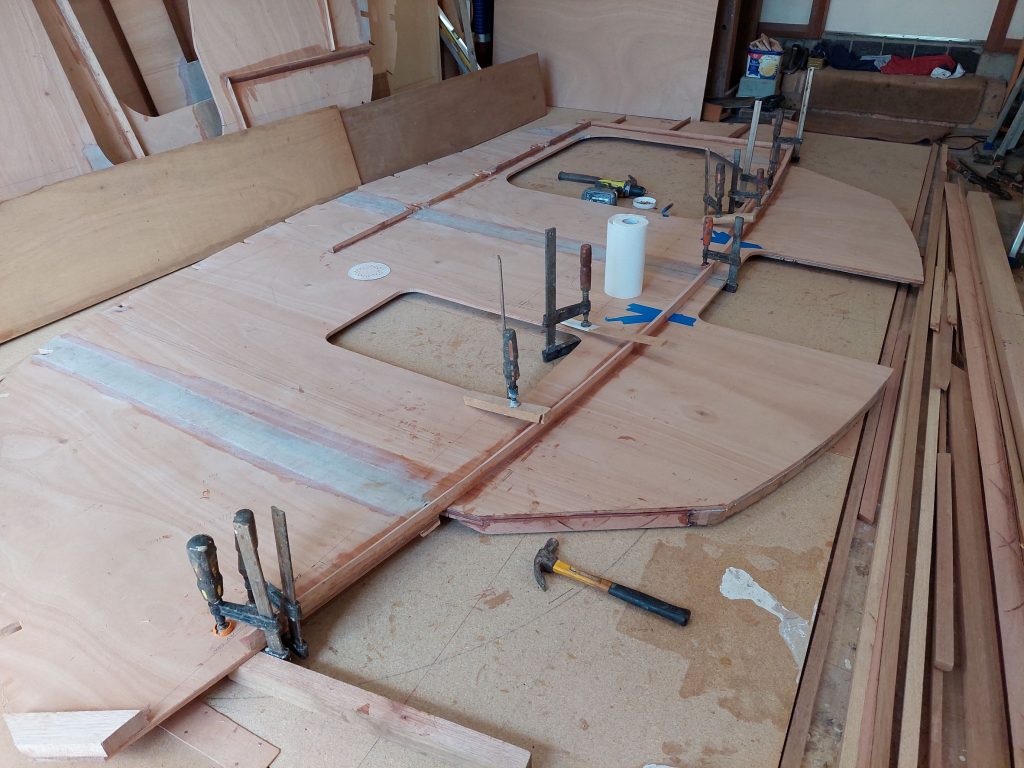
After four months isolated from our family due to Covid 19 movement restrictions we were able to visit our Sydney based family on Sunday and dine in the evening with local friends. Those activities took precedence over boat building or sailing so a return to swinging off the side of the Laser was delayed for another week. Sunday was a great sailing day at Middle Harbour where 30 Laser sailors from various clubs met on the water at Middle Harbour and it will be good to join them in the near future.
Meanwhile back in the shed another bulkhead, bulkhead D, has been fitted with furniture cleats and bulkhead E is well on the way. With only so much room on the floor of the garage I took the afternoon off to chase up my major timber purchase and procure a little more to keep me going.
That done it was still a fine afternoon so I turned my attention to the building frame.
When I built the frame for Passion X only the best materials were used so consequently the frame needed very little attention to bring it back to working condition. Over the years I have used up any left over epoxy glue to seal the timber on the building frame and part of today’s job was grinding all that epoxy resin back to a flat surface.
Tomorrow I am doing an urgent Category 4 audit but despite the boat building time lost to visit the club I think that bulkhead E will be finished and I will have a session cutting up timber for more furniture cleats and for the big laminated post under the mast. I am thinking of laminating in a ribbon of carbon fibre on the centre line of the mast post as a permanent line just for show.
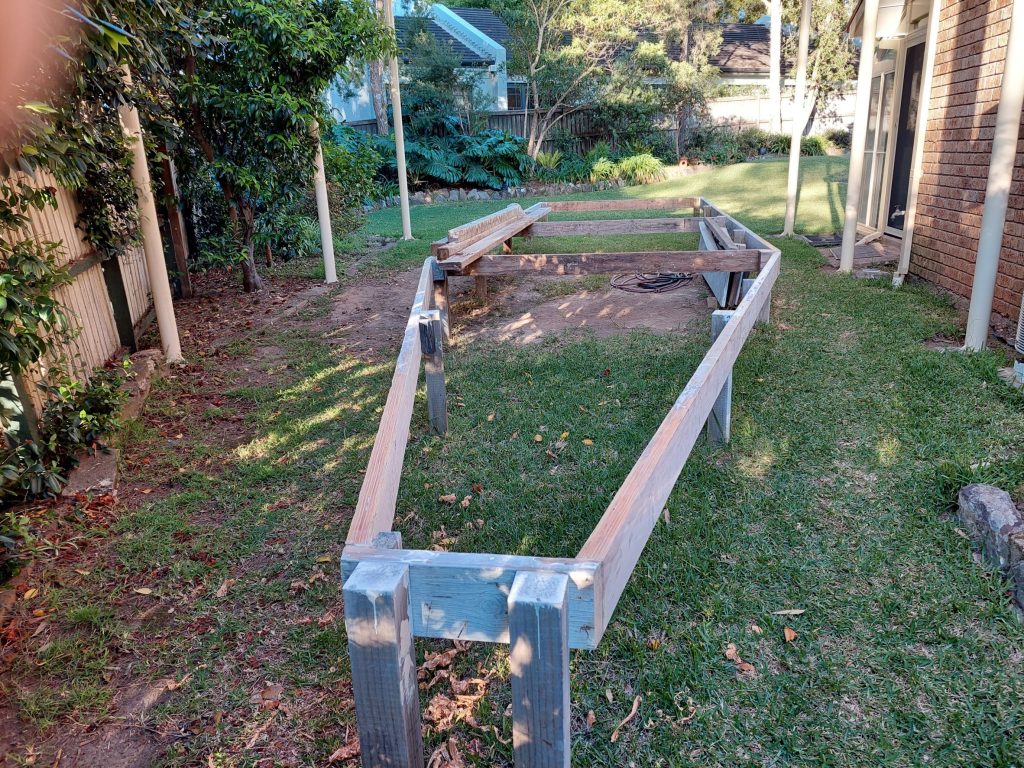
The first Saturday for post Covid 19 sailing was a windy one but not that it mattered. I had already decided that I would work on the new Passion as I am enjoying the project. As I work through the details I remember little things that I have on Passion X that I would have done differently. I recall standing bare footed on a V berth cleat and thinking that that was a bit sharp and so on the new Passion I am making tiny but for me material changes. Also the time pressure is not there and I can spend more of it in finishing touches so that there will be less finishing later in the project.
I am planning on a few mass production efforts where every bulkhead is painted at once rather than the one by one process on Passion X so I know that there will be some catch up time to compensate for my attention to detail now.
For the record I stood up station 0, bulkhead A and bulkhead B for a photo opportunity as they are completed. Bulkhead C could not come to the party because the epoxy glue was still curing but she is finished too. Also finished are the transom and the Aft Perpendicular which is a fancy way of saying the last little bit of overhang that forms the boarding step.
Next on the list in order of priority is bulkheads D, E , F, H, J, and K all of which are in semi finished state and need at most a day to complete. It is not quite that easy as there are furniture cleats to be fitted to both sides of most bulkheads and I have room for one at a time.
What is pleasing is that half of the bulkheads are now finished except for the final detail around the keel support. Dudley’s strong back on this yacht goes from Bulkhead C all the way back to Bulkhead H and is going to be an impressive I beam for the engineering minded.
On Passion X the keel structure is pretty impressive already and one of my professional boat builder friends opined that the keel structure would be an archaeological find for future generations. I cannot wait to see what he says about the new structure.
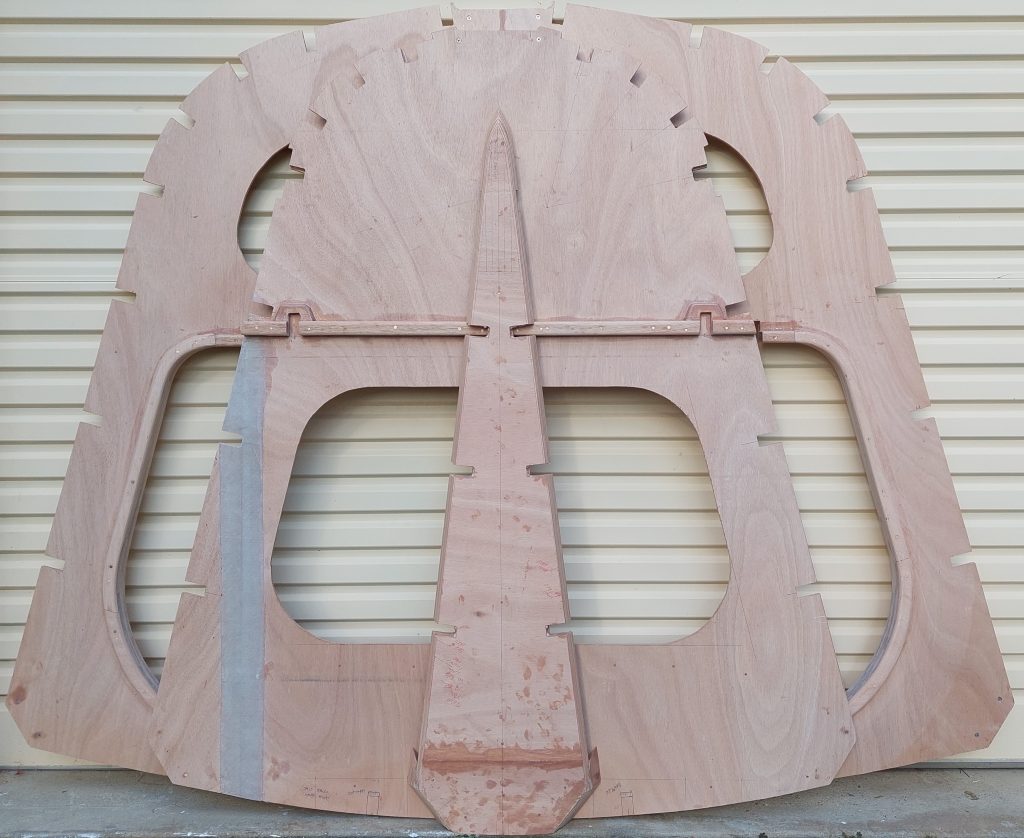

Today was the first official post Covid 19 race from the Balmain Sailing Club and it turned out to be an exciting one. Pre start the wind and rain came through in waves so we had already decided to sail with a reef in the main and the No 3 jib by the time we arrived at the club.
DJ joined us for the day and Elaine was relieved to have a strong male on board to help with crew duties. From the start it was a balancing act to find a groove with enough height but not too much heel. Our almost full water tanks helped to make up for the small crew numbers and we trucked along in the 20 knot breeze quite nicely. As we pulled away from the yachts that started with us I though we must be the only yacht with a clean bottom. Whatever the reason we were pleased to be overtaking and to be creating distance between the back markers.
From Spectacle Island to Goat the breeze hotted up and we saw regular hull speeds of over nine knots. Just off the navigation mark at Goat Island the wind hit 30 knots and we surged and popping up momentarily to 12.2 knots.
That was the last of the downwind excitement as we had to turn away from the breeze to sail into the wind shadow to leeward of Goat Island.
Little by little we drew up to the Jeanneau 409 only to have them jump out again. They were sailing well to windward and as the breeze had freed a little there were no overtaking opportunities. Our lucky break came at our next approach to Spectacle Island where we had obstruction rights in the narrow channel.
No sooner had we passed the 409 the breeze died down to seven knots. They with full mainsail seemed to be catching so we shook the reef out and held our slim lead to the finish.
I am sure next week will see a lot of yacht return to form as they clean their hulls ready for the first of the races where points count. Our hope is that todays result will not affect our handicap for next week
Yesterday was a very productive day as far as visible progress goes. I have had seven cabin beams laminated up for several weeks waiting for the right time to fix then to bulkheads. With the part complete bulkheads up off the floor I tackled the task of removing all the excess epoxy glue from the laminated beams. Once clean enough to go through the thicknesser they were all dimensioned down to 29 mm. This is two mm thicker than on Passion X and well above specification.
The next task was to router the edges of the beams up to the point where they join to the bulkheads and no further. In one day I managed to attach three roof beams and other cleats which seemed like good progress but it was more the culmination of scheduled work.
Today we had a scheduled power outage from 7:30 am to 4:30 pm and it went the whole distance. In anticipation I had used the time yesterday to cut some lumber some of which did get used today.
Mid morning with bulkheads stacked up against the wall again I saw the empty floor and promptly dragged out bulkhead B for more work.
Bulkhead B is mid way along the v berth and is designed to have a moulding around the edge of the 9mm plywood frame for comfort. The prospect of rolling into a 9 mm wide plywood edge while rocking around at sea is not one that would be welcome. Many options were contemplated but the one I settled for could be produced with my battery operated jig saw and a lot of time. Many 25 mm wide shapes were cut from 9 mm ply and by nesting the shapes very little plywood was used. To improve the uniformity of the strips they were clamped together and shaped to the same dimensions.
I now have a beam made up of five layers of 9 mm ply and after rounding the edges it should provide the necessary level of comfort while at the same time producing a very still and strong cabin beam.
I am a fan of reinforcing on the internal edges of plywood frames for durability and this one on Bulkhead B in the middle of the V berth gave me as much satisfaction as the three bulkheads completed the day earlier.
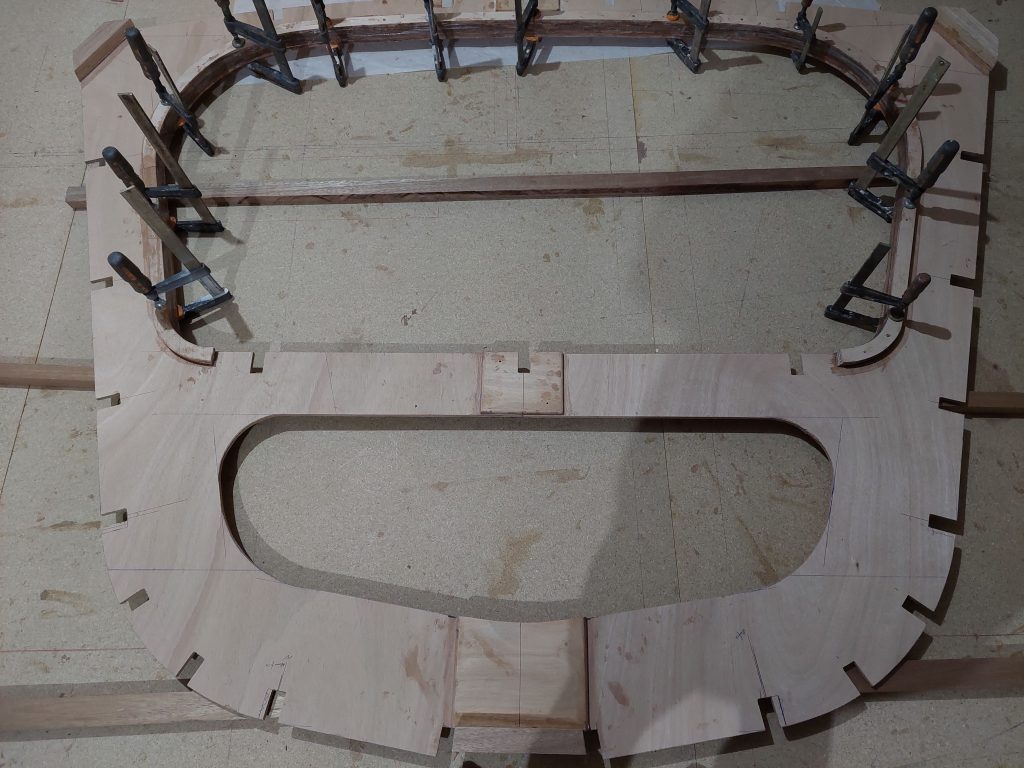
With only half of the garage floor available for construction the progress on the bulkheads has been very sequential. The warmer weather of October spring has accelerated the epoxy resin cure and on some days two gluing sessions have been possible. One before coffee in the morning and one after dinner in the evening.
Today I tried the double decker method where the first epoxy lamination was covered with my favorite gluing aid, oven baking paper, and the second bulkhead placed on top. Not only did that work well but the day was warm enough for a second session before dinner.
In between laminating sessions I carried bulkheads into a shaded part of the garden for routing, sanding and marking up. I would call this al fresco boatbuilding, a term stolen from my sailmaking friend, Ben Gemmell who has done a bit of sailmaking in the garden during Covid lockdown.
While working in the garden a friendly lizard visited to make a close inspection and I did manage to capture his visit on camera.
All in all it was a pleasant productive day



A month after the plywood arrived I have finished cutting all of the bulkheads and have them stacked up against the wall of the garage. Allowing that the thickness ranges from 36 mm on parts of the transom to 9 mm for the lightest frame the full pack of bulkheads occupies very little room. So thin is the pack of frames that it is deceptive that this will expand out to a 12 metre yacht.
Now it is wrong to say that the bulkheads are finished as I still have to attach all the timber cleats to which the longitudinal structure will be fixed and that needs a delivery of timber and a lot of cutting. On the plus side I have marked all the frames with the location of these timber cleats so that the process of completing them should be quite straight forward.
One of the advantages of building a similar yacht is that I have good photographs from the first build and can recall the parts of the construction that were difficult. Perhaps difficult is not the right word. Perhaps it would be more correct to say that having done it one way I can see a better way the second time. I am taking more time to fair cut lines to exactly the design mark as I have more confidence it will be exactly correct. It also helps that the Naval Architect is providing very precise drawings with more detail that enables more precise location of the stringers. As well the PDFs can be exploded and unknown dimensions checked to a very close tolerance. The combination of the lines plans and the hull and deck lines gives a very accurate location of all the construction lines.
Unfortunately there will be very little to show for the next few weeks of finishing the bulkheads and cutting the strongback and stringers. Add to that the anticipation that we will be more mobile and able to return to active sailing rather than just daydreaming about it while cutting frames progress is likely to slow a little.
And while progress might slow as life returns to normal I will be able to look back at the lockdown and reflect on how it crystallized my ideas for a new yacht, engaged a Naval Architect and progressed the plans fast enough for me to cut a full set of bulkheads.
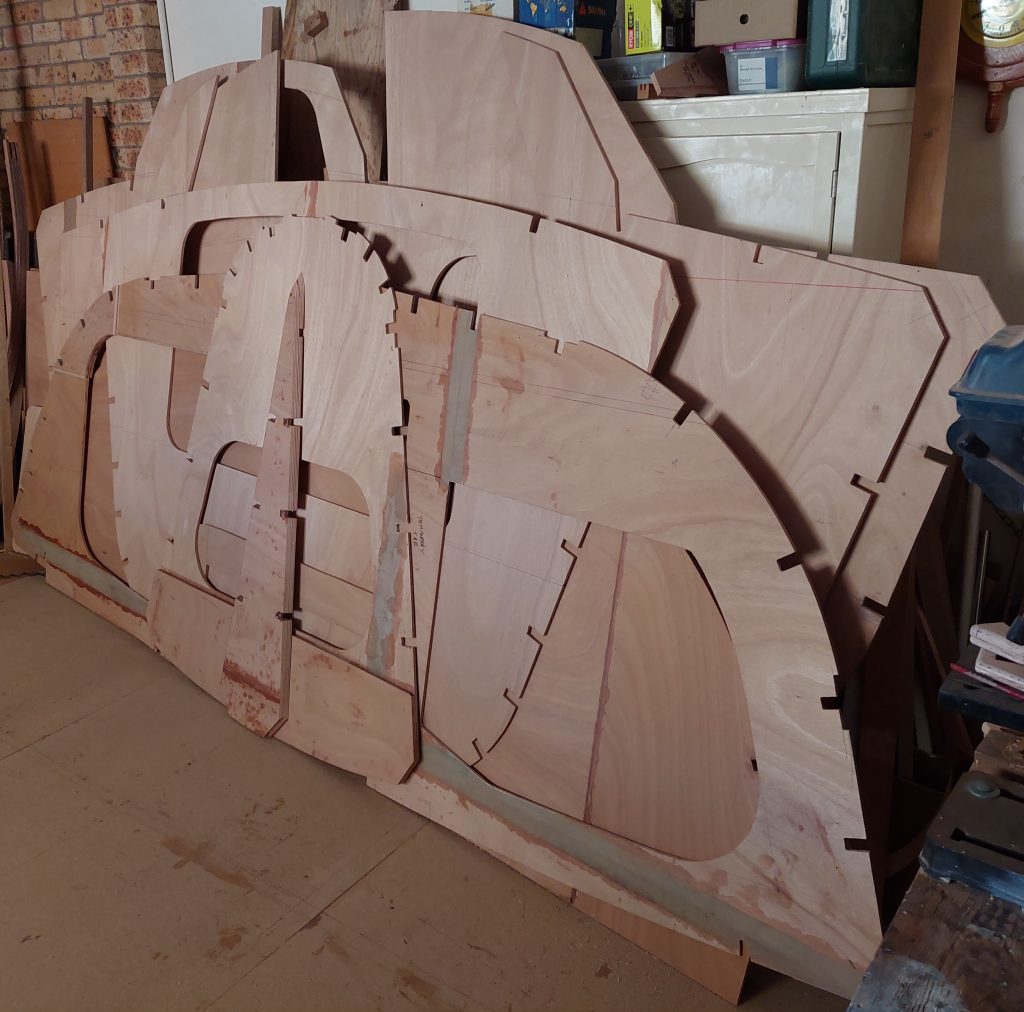
A day after my last post I cut the first bulkhead for the new yacht. Not daunted by the size of the frame I started with the largest which is 3.8 metres wide. This is the bulkhead at the aft end of the cabin and inside it forms the entry to the quarter berth. In just in time fashion the communications with the naval architect arrived agreeing on the width and location of the quarter berth opening and as soon as it was cut correctly a drawing arrived in perfect agreement. In similar fashion I have worked from the transom to the cabin adjusting cut outs for the wider yacht and leaving more meat in the frames to allow for the wider spans. Once the scantlings are completed there may be scope to trim back some of the frames but I am pretty happy with the sizes as they look suitably proportioned for the larger interior.
As of today I have five frames cut and on some the process of adding reinforcing has begun. Based on the current rate of progress it is possible that in three weeks all the bulkheads could be completed but there are some roadblocks. I need to get my head out of the sawdust and epoxy resin fumes and order in some essential supplies. You would thing this an easy task but when one is addicted to the smell it is not so easy.

As we are more than 5 km from any water sailing is out of the question. For the first few months of the Delta wave we were permitted to do maintenance on the yacht. On the water at Greenwich was a pretty civilized way to spend an afternoon and several useful jobs were completed including improving the finish on the vanity in the head. As for sailing gear I did install roller bearing cheek blocks for the mainsheet instead of the plain bearing organizer and am keen for a race in earnest to see how effective it has been.
As the virus has been getting more out of hand in Sydney we have been told that even moving in isolation to the yacht and doing maintenance in isolation is not allowed.
Fortunately I had started on plan B for our next yacht and accelerated the program. That has given me hours of pleasure pouring over plans and alternative designs to finalize the brief and get the design started.
At this stage as reported last blog I have finished the winch bases and now with the passage of eleven days completed laminating all the cabin beams.
With the arrival of 1.4 tonnes of plywood on Thursday I have painstakingly set out the garage floor ready for mass production of bulkheads. I was surprised how easy it was to lift the chipboard floor we used for Passion X, turn them over and refix them with clean faces upwards. The first step was to practice setting out frames and making the tool that would make the process less time consuming. Chief among these are a 3.9 metre straightedge and similar length timber batten for marking out deck crowns. A large plywood square with a 55 degree angle for setting out the cabin sides will also be a useful time saver. Finally a clear plastic template for marking stringer cut outs speeds up the process.
One day of practice and one day to lay out the real thing has resulted in the largest bulkhead being laid out ready for cutting and gluing the sections together. I suspect it will take up to four days to a week to complete each frame so I have quite a length of runway ahead before anything emerges into the open.
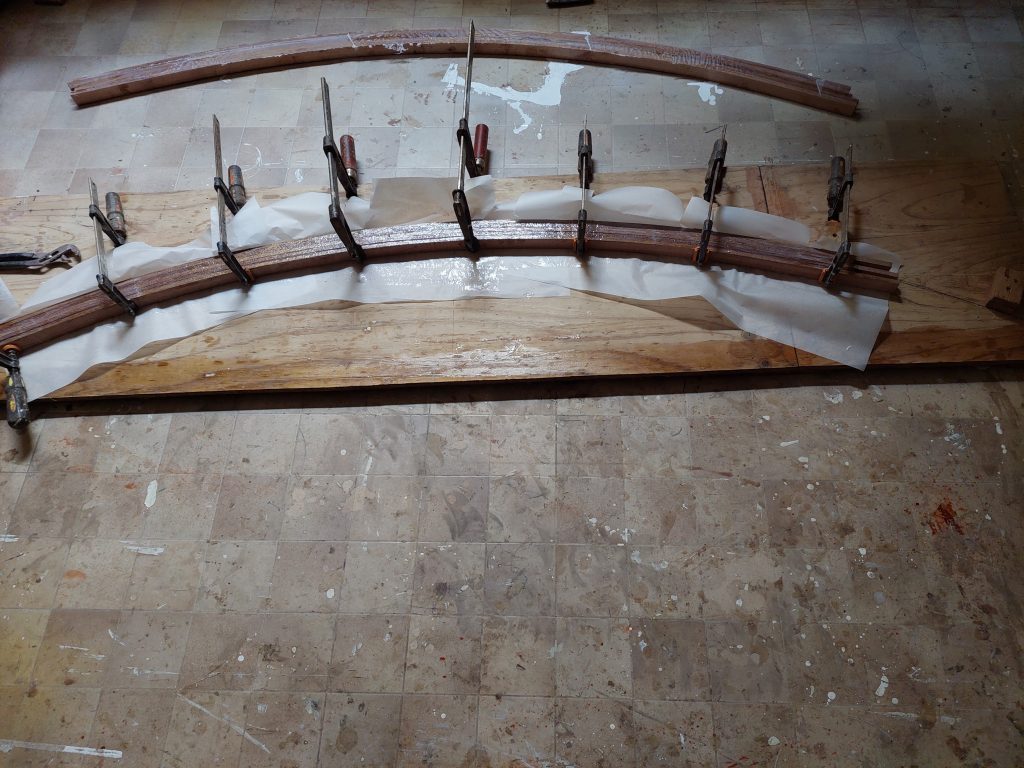