I have been busy. Last weekend was the Laser state titles at Wangi Wangi which kept us occupied for two days and away from boatbuilding. A rest from boatbuilding was needed as the overuse injuries are starting to mount up and I am having to pace myself with the manual labour. Still a lot has happened and so this will be a catch up blog.
First the yacht racing where we scored a third and a first place in the last two Wednesday events. The first place was last week when we were given second on the night but the winner must have overlooked his crew list. No big deal as we all move up one point and the series stays in the same order. It was one of those nights where if you get out of Humbug early you establish a good lead and that is what we did. It is a rare race indeed when we beat the Sydney 38 Utopia by quite a few minutes. Congrats to Adrian for fastest time and commiserations to Steve who was second fastest on the night.
On the boat building scene I spent the Thursday and Friday prior to the Laser regatta trimming the excess plywood from the gunwales. This is an awkard job as the angle is uphill so by the end of two four hour sessions my arms were pretty tired but I am very pleased with the result.
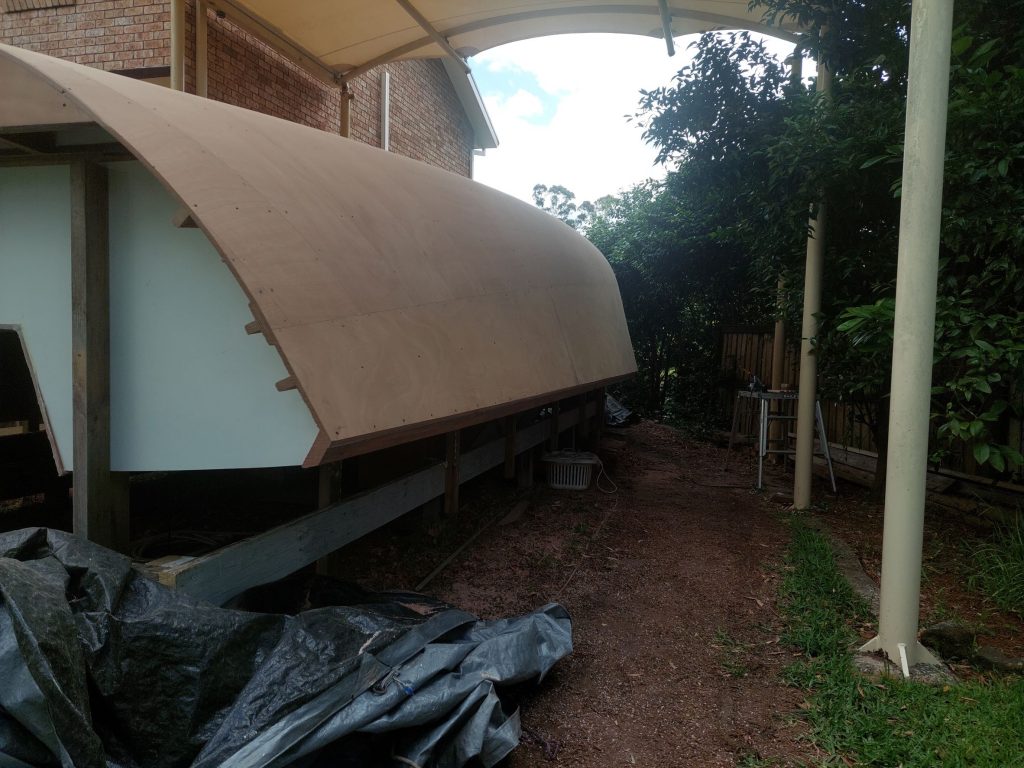
My engine beds were delivered saving me a long trip and after a few trial fits and epoxy coating or the timber base the metal angles are firmly bolted in their final position.
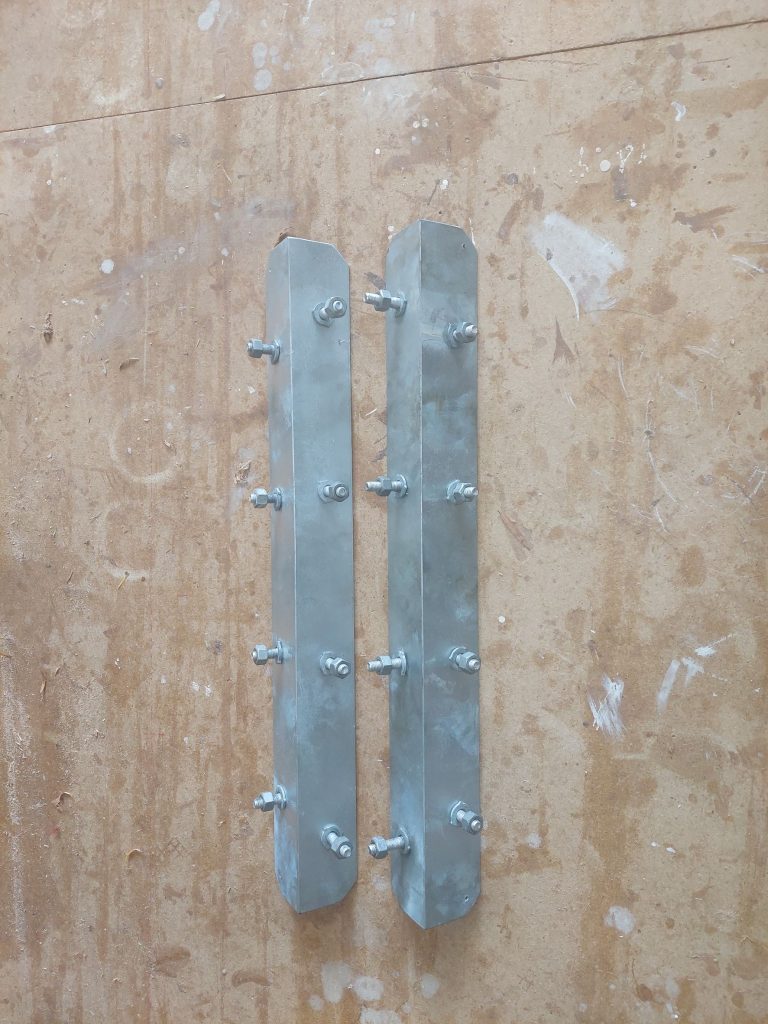
One of the achievements of the past fortnight was to manufacture an epoxy glass stern tube which is twice the thickness of the off the shelf items. I had an ideal mandrel in the form of 32 mm OD fibreglass pultrusions with a highly polished surface. I did have to use the one tonne chain block to extract the mandrel but the result is very pleasing.
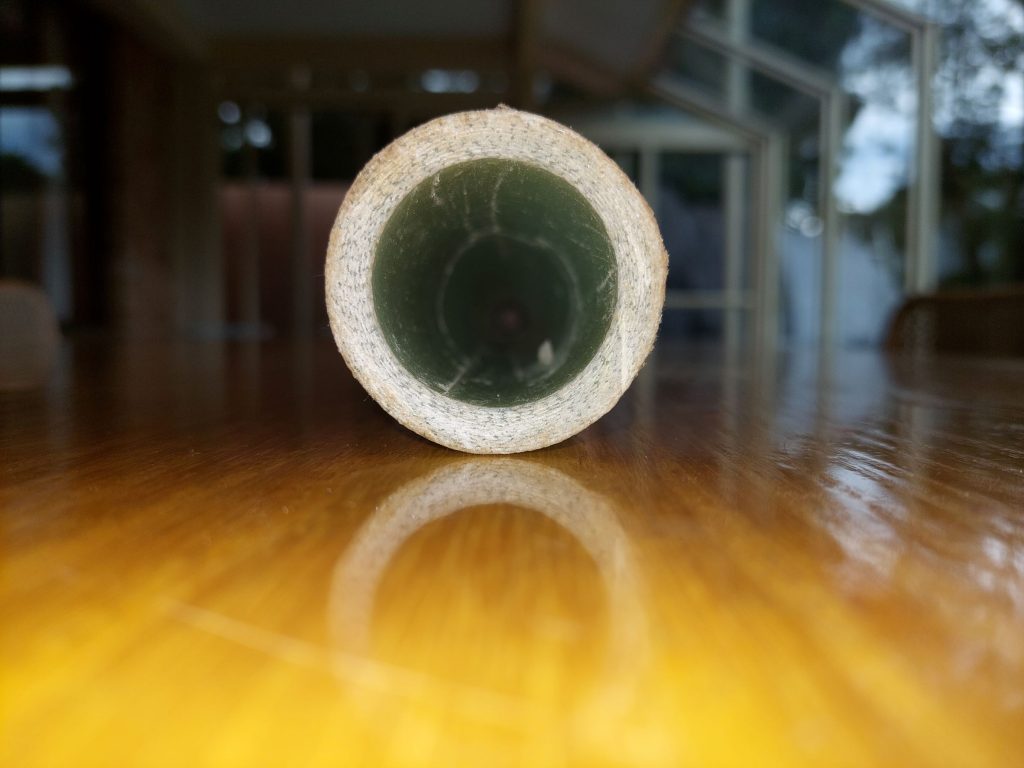
On Thursday I collected my drive train components and on Friday and promptly bedded in the P bracket and stern tube using the bearings dry fitted as alignment guides.
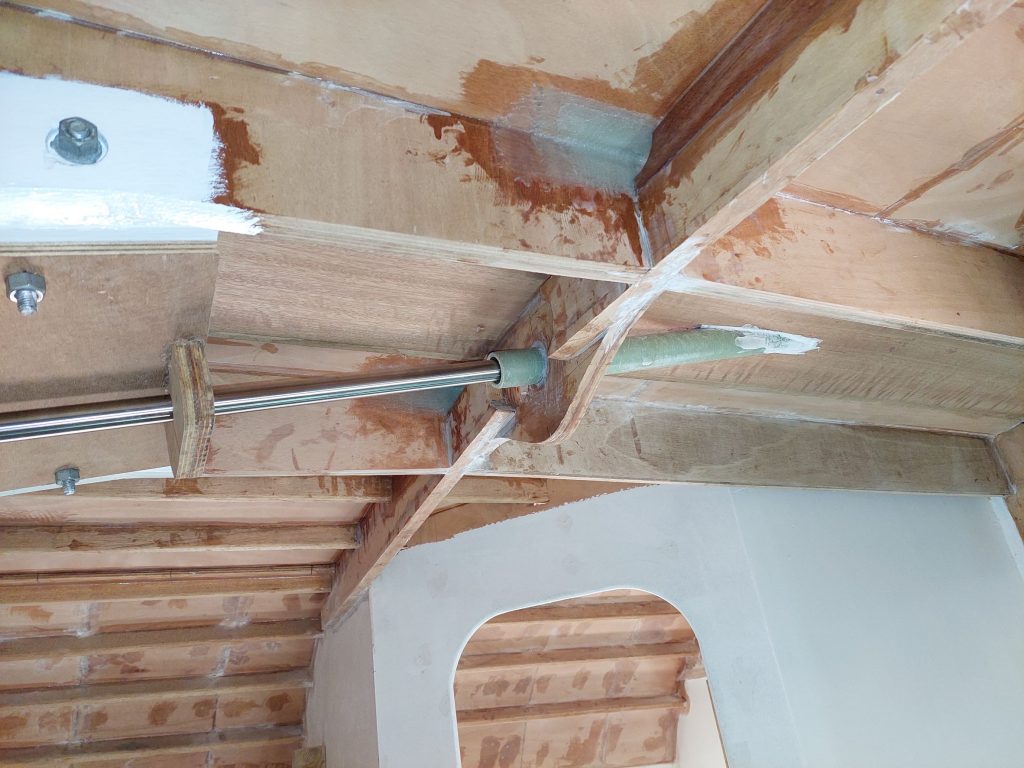
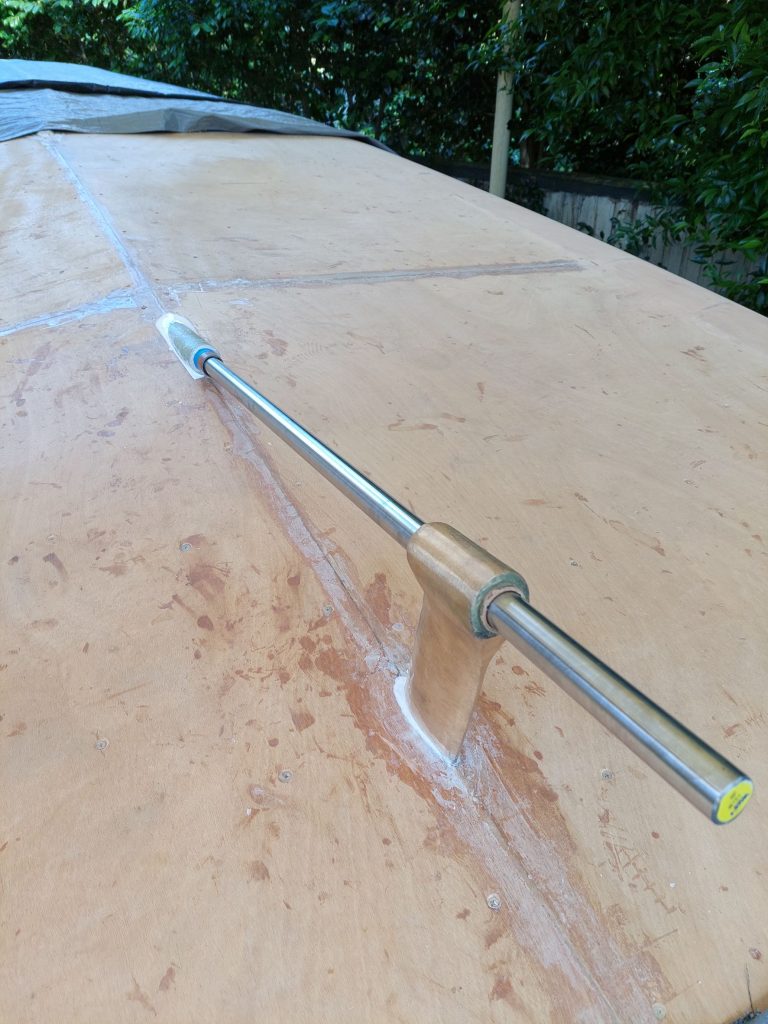
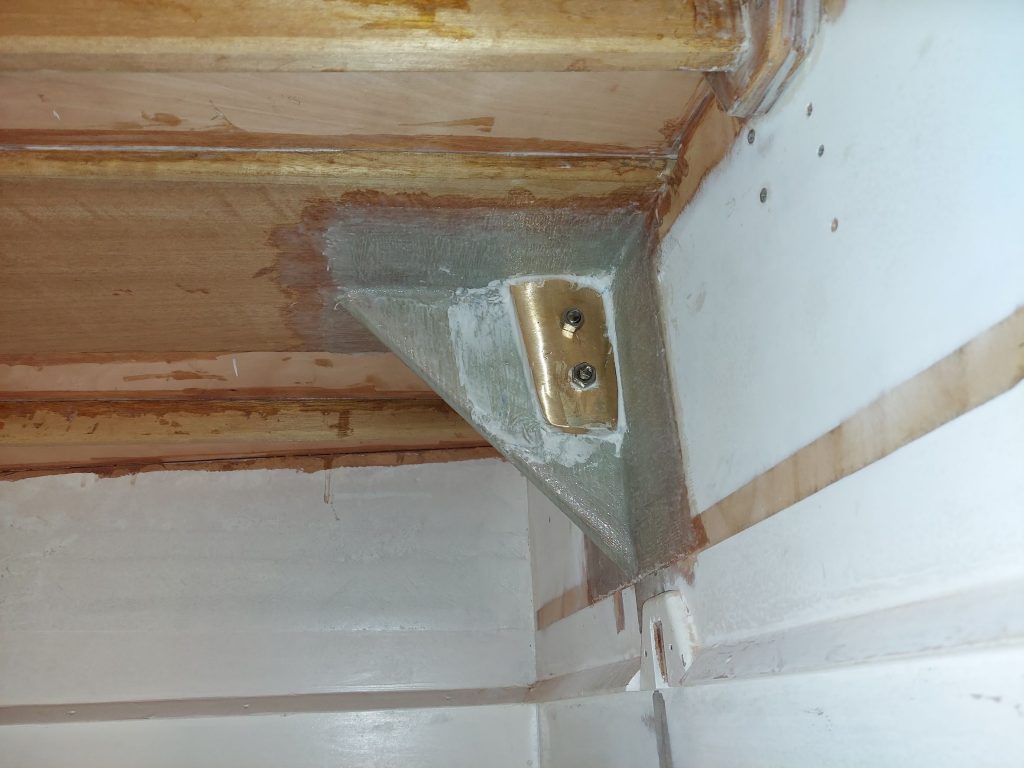
On Friday I cut out the holes for the rudder stock having previously reinforced the hull with 24 mm of plywood attached to the 12 mm skin and fixed between the strongback and the stringers. The cutting was accomplished with the required diameter hole saws in very quick time. A post cutting alignment check was conducted mainly to get the tiller stop on the upper housing exactly on the centre line.

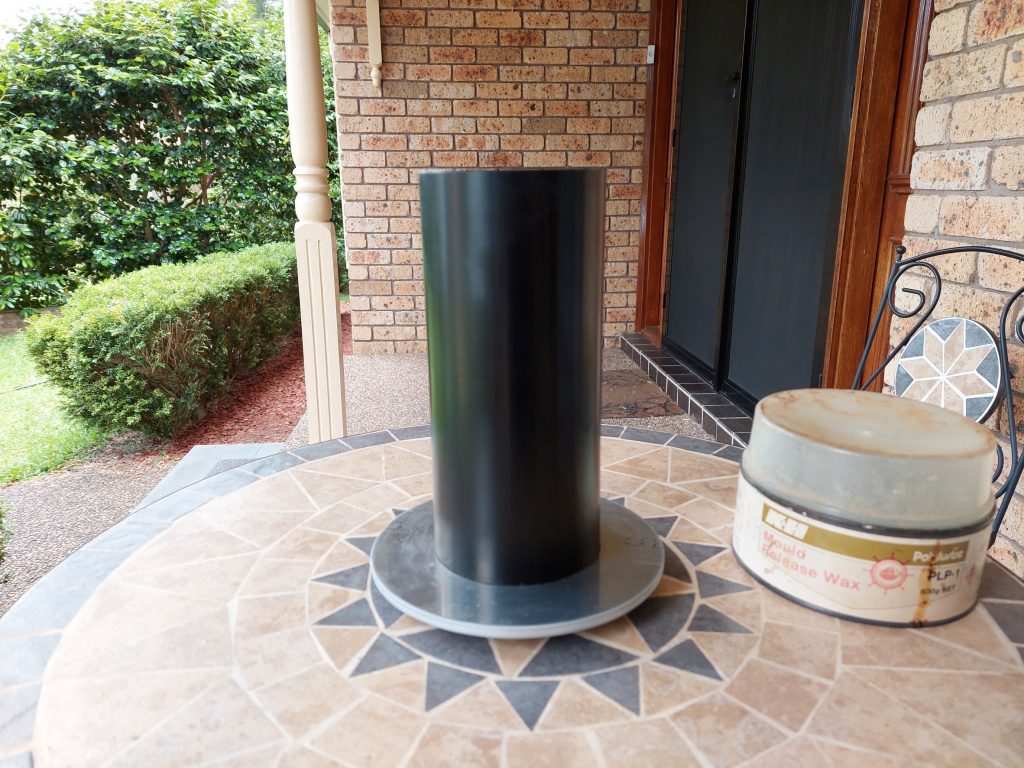
The lower bearing housing has been fabricated and after a couple of days the mandrel will be pressed out of the moulding leaving me ready to fix the rudder stock position.